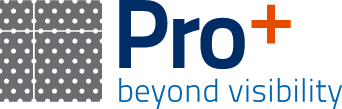
Pro+ is the perforated Aluminium screen solution by Endurescreens – providing the most advanced seam matching technology available today. Pro+ is the only high-quality solution for creating a continuous images for various applications ranging from dome theatres to planetariums as well as for architectural installations – anywhere a uniform surface is needed that can be creatively lit and is used for projection. Additionally, Pro+ provides acoustic transparency that enables airflow through the screen. We take great pride in the quality of our products and given the experience and superior results of Pro+, the overlapping panel seams or powder coating are not an option for our clients. Pro+ will improve your image in many ways.